In the pursuit of efficiency and health today, personalized medical and rehabilitation solutions are gradually permeating every corner of our lives.
Among these, orthotic insoles stand out as an important aid for alleviating foot problems and enhancing the walking experience, and their manufacturing technology is undergoing an unprecedented revolution. This article will take you on an in-depth exploration of how advanced foot scanners can capture 3D data and how 3D printing can be used to create precise orthotic insoles, ushering in a new era in their production.
Traditionally, the production of orthotic insoles relied heavily on manual measurements and experiential judgment, which was not only time-consuming and labor-intensive but also made it difficult to meet each patient’s individual needs with precision.
Now, with the rapid development of technology, especially the mature application of 3D scanning and printing technologies, the production of orthotic insoles has entered a new age of intelligence and precision. This transformation has not only significantly improved production efficiency but has also made the corrective effects more noticeable, truly achieving a shift from “fitting the foot” to “fitting the need.”
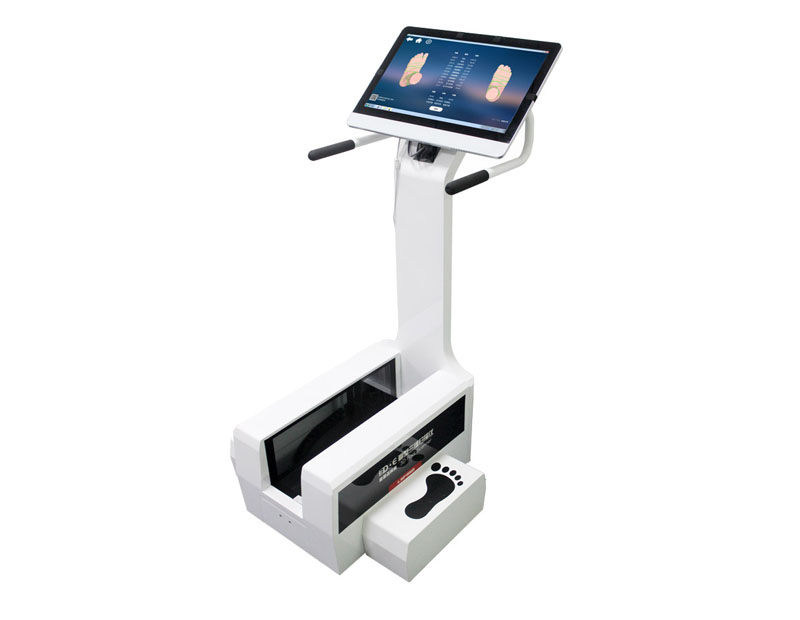
3D Foot Scanners: Precisely Capturing Every Detail
At the first step of producing orthotic insoles, high-precision foot scanners play a crucial role.
These advanced devices use non-contact optical scanning technology to rapidly capture the three-dimensional shape of the patient’s sole, including the height of the arch, width, length, and subtle variations in contours. This data is presented in point cloud form, providing detailed and accurate foundations for subsequent 3D modeling.
More importantly, 3D foot scanners can capture dynamic changes during a patient’s gait, such as gait analysis and pressure distribution, providing scientific basis for customizing correction plans. This comprehensive, multi-dimensional data collection method ensures that the design of orthotic insoles precisely matches the actual needs of patients, achieving a true “custom fit.”
3D Printers: Transforming Digital Models into Reality
After obtaining precise 3D data, the next step is entrusted to 3D printers. These high-tech devices can print orthotic insoles that perfectly conform to the patient’s sole shape by layering materials according to pre-set model files.
Compared to traditional handcrafting, 3D printing offers higher precision, greater repeatability, and faster production speeds. Additionally, it allows for flexible adjustments to the physical properties of the material, such as hardness and elasticity, to meet the diverse needs of different patients.
Personalized Correction, Rebuilding Healthy Steps
Through the combination of 3D foot scanning and 3D printing technology, the production of orthotic insoles achieves unprecedented personalization and precision.
Whether dealing with congenital foot conditions like flat feet or high arches, or chronic fatigue and pain due to prolonged standing or walking, customized orthotic insoles can effectively alleviate these issues.
These insoles not only correct poor foot posture and reduce joint strain but also help prevent other body problems caused by improper gait, such as knee pain and back discomfort.
With the continuous advancement of 3D scanning and printing technologies, the field of orthotic insole production is experiencing unprecedented opportunities for development. It not only brings more comfortable and efficient correction experiences to patients but also injects new vitality into the medical rehabilitation industry.