Application process and principle of 3D foot scanner in the production of corrective insoles
1. Data acquisition and modeling
Use structured light/laser technology to quickly capture the foot shape (standing or sitting) and generate a three-dimensional model with millimeter-level accuracy, including key data such as arch height.
Identify abnormal foot types such as flat feet and high arches.
Data processing and analysis
The software automatically calculates indicators such as arch height ratio (AHI) and calcaneal valgus angle to generate a visual report.
Adjust model parameters (such as arch support height and forefoot buffer thickness) in combination with medical needs to provide a basis for personalized design.
2. Corrective insole design
Biomechanical correction scheme
Design support structure based on scanning data:
Flat feet: Enhance arch support and disperse heel and forefoot pressure.
High arch feet: Add forefoot buffer layer to reduce metatarsal pressure.
Inversion of the foot: Adjust the inner and outer height of the insole to correct the force line of the lower limbs.
3D model optimization
Use professional software (such as CAD) to adjust the model in detail to ensure that it fits the foot curve.
Output in STL, OBJ and other formats, suitable for 3D printers or engraving machines.
Foot 3D scanner
III. Manufacturing and verification
3D printing/engraving processing
Material selection : Select elastic materials such as EVA foam, silicone, nylon, etc. according to needs to balance support and comfort.
CNC engraving : The engraving machine accurately cuts materials according to the model to form customized grooves and convex structures.
Try on and adjust
After the user tries on, evaluate the comfort and correction effect, and optimize the insole design (such as local thickening or thinning) by fine-tuning the model parameters.
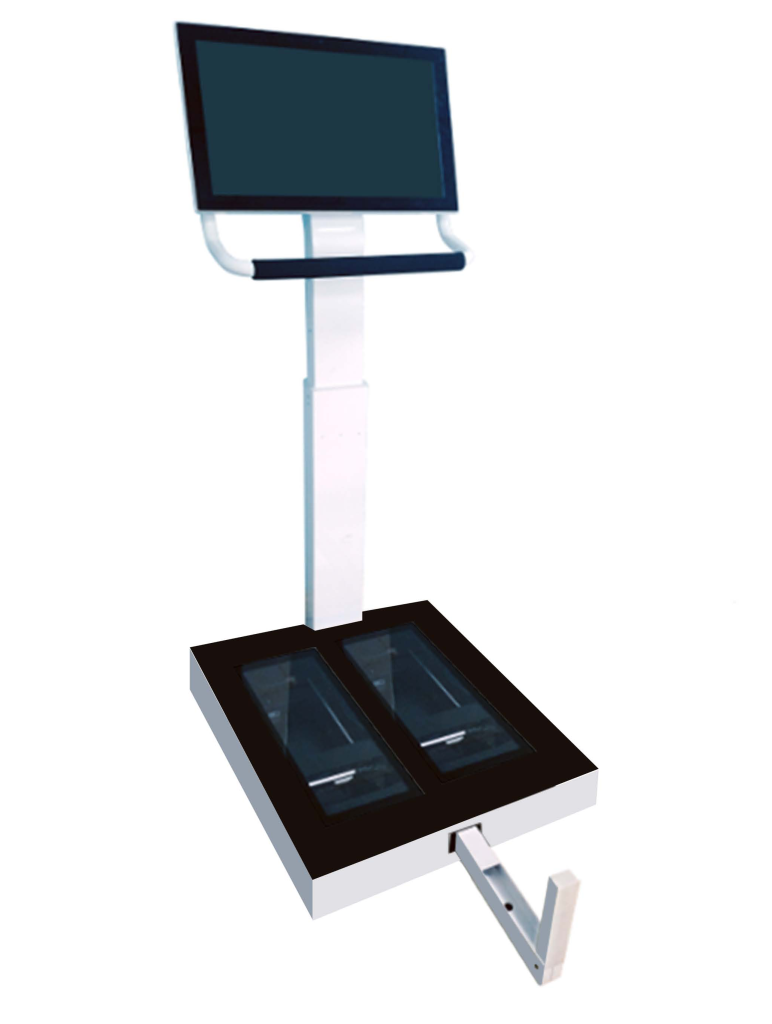
IV. Application advantages
Personalized customization : Accurately match individual foot characteristics to solve the adaptation problem of traditional insoles “one insole for a thousand people”.
Precise correction : Optimize the support structure through biomechanical analysis to reduce the risk of joint compensation injury.
Efficient production: The whole process is digitalized, and the production time of a single pair of insoles can be shortened to 2-4 hours.
V. Typical application scenarios
Medical rehabilitation: auxiliary treatment of chronic diseases such as plantar fasciitis and Achilles tendonitis.
Sports medicine: optimize the force of athletes’ feet and prevent sports injuries.
Children’s foot development: regular scanning to monitor the development of the arch and timely intervention of deformity risks.
Precautions
The correction plan needs to be guided by a rehabilitation physician or foot and ankle specialist to avoid secondary injuries caused by self-design.
Children need to be re-scanned every 3-6 months to adapt to the growth changes of the foot.
Through 3D foot scanning technology, the production of corrective insoles has achieved an upgrade from experience-based to data-driven, significantly improving wearing comfort and treatment effects.