Application process of plantar pressure tester in the production of corrective insoles
1. Data collection stage
Static and dynamic pressure detection
Static test: Through pressure sensing pads or sensor matrices, measure the pressure distribution of various areas of the sole when standing, identify structural abnormalities such as flat feet and high arches, and locate high-pressure areas (such as the inner side of the sole or forefoot).
Dynamic test: Monitor pressure changes during walking, running and other actions, analyze the force characteristics of heel landing, midfoot support and forefoot push-off stages, and capture gait abnormalities (such as inversion/external rotation).
2. Data analysis and program formulation
1. Abnormal pressure point identification
The system generates a heat map to quantitatively display the distribution of high-pressure and low-pressure areas, and determine the key areas that need to relieve pressure (such as metatarsal heads or heels).
Combined with gait cycle data, evaluate foot stability problems (such as excessive internal rotation or external rotation) to provide a basis for correction design.
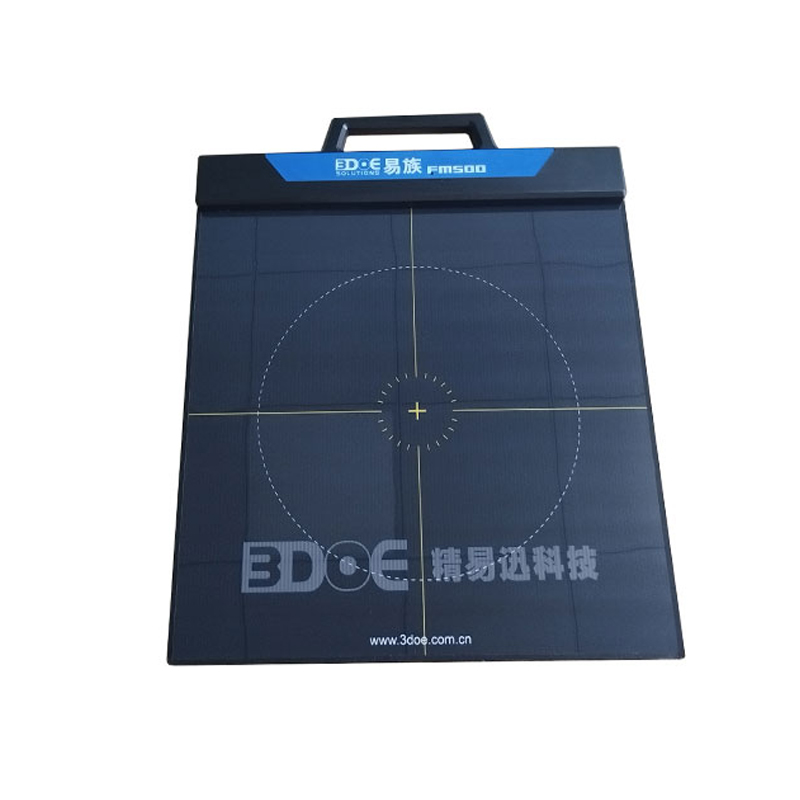
2. Personalized parameter design
According to the pressure distribution and arch shape, calculate the parameters such as the support height, material density (such as EVA or TPU) and thickness distribution of the insole.
For example, patients with high arches need to increase the arch support height to reduce the tension of the plantar fascia, while flat feet need to evenly disperse the forefoot pressure.
Plantar pressure distribution system
III. Insole production and verification
1. Digital molding technology
Use 3D printing or CNC engraving equipment to complete the initial molding of the insole substrate based on the data model to ensure accurate matching of the foot shape.
Optimize the edge curvature and contact surface smoothness through manual polishing to improve wearing comfort.
2. Functional verification and iteration
After the patient tries on the shoes, the correction effect (such as the degree of improvement in pressure distribution) is tested again by the pressure tester, and the insole design parameters are adjusted according to the feedback.
For example, when the dynamic test shows that the forefoot pressure is reduced by 30%-50%, it indicates that the correction plan is effective.
IV. Technical Advantages
Accuracy: The sensor array captures tiny pressure changes to ensure data reliability.
Personalization: Customized insoles based on foot shape and pressure data to relieve pain and improve gait.
Efficiency: A single scan takes less than 10 seconds, and data collection and design are completed quickly.
Dynamic Monitoring: Real-time feedback on correction effects, supporting multiple iterations of optimization.