The difference between 3D printed insoles and 3D engraved insoles
1. Technical principle and production method
3D printed insoles: After obtaining three-dimensional data through plantar scanning, the model is optimized using computer-aided design (CAD), and the material (such as PA12 nylon, TPU, etc.) is stacked layer by layer directly through a 3D printer to complete the production, relying on automated equipment throughout the process.
3D engraved insoles: Based on the scan data of the plantar scanner, the model is optimized using computer-aided design (CAD), and the raw materials are cut and processed by an engraving machine. It also belongs to the automated production of insoles, but the materials and tools used are different.
2. Precision and personalization
Both 3D printing technology and 3D engraving can achieve millimeter-level precision, ensuring that the insole is highly fitted to the foot, and support complex morphological designs such as lattice structures, improving breathability and mechanical properties.
It’s just that the applicable materials are different, and you can choose the right equipment according to user needs.
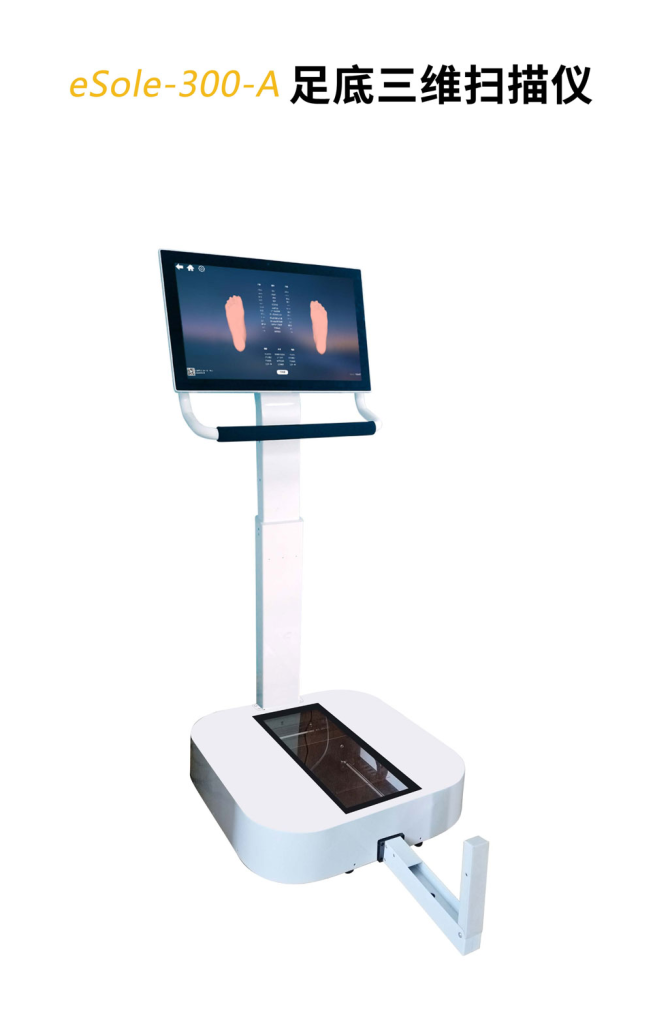
3. Materials and functional characteristics
3D printing has more optional materials, such as elastic materials with memory function (such as patented EM materials), breathable nylon, etc., taking into account support, resilience and comfort.
3D engraving mostly uses traditional hard materials, with small functional adjustment space, weak breathability and long-term durability.
The core role of plantar scanners
Data collection: Through non-contact three-dimensional scanning technology, accurately obtain plantar morphology and 3D data, and the error is controlled at the millimeter level.
Personalized design basis: Scanning data provides a basis for subsequent CAD modeling, such as adjusting the arch support point, optimizing the force distribution, and ensuring that the insole meets the user’s specific needs (such as correcting gait and relieving pain).
Efficiency improvement: Replace traditional manual measurement, shorten the customization cycle and reduce human errors, and promote large-scale customized production.
Both 3D printed insoles and 3D carved insoles have become mainstream trends with their high precision, strong functionality and material advantages. Plantar scanners, as the common technical starting point for both, lay the core data foundation for personalized customization through digital means.