In the fast-paced modern life, more and more people are beginning to pay attention to foot health. After all, our feet not only bear our weight, but also affect the overall mechanical balance of the body. If you want to have comfortable and fitting insoles, it is far from enough to rely on ready-made styles. Today, let’s talk about how to use the sole 3D scanner combined with 3D printing technology to create a pair of truly exclusive personalized insoles for yourself.
1. Start with understanding your feet
Everyone’s foot shape is unique. Some people have high arches, some have flat feet, and some have slight inversion or valgus. If you don’t consider these differences and blindly choose insoles, not only will you not be able to achieve the effect of support and protection, but you may even increase the burden on your feet.
The sole 3D scanner is the first step to solve this problem. Through high-speed scanning, the device can accurately capture every contour detail of the sole of the foot in a few seconds, including the curvature of the arch, the arrangement of the toes, the width of the sole, etc.
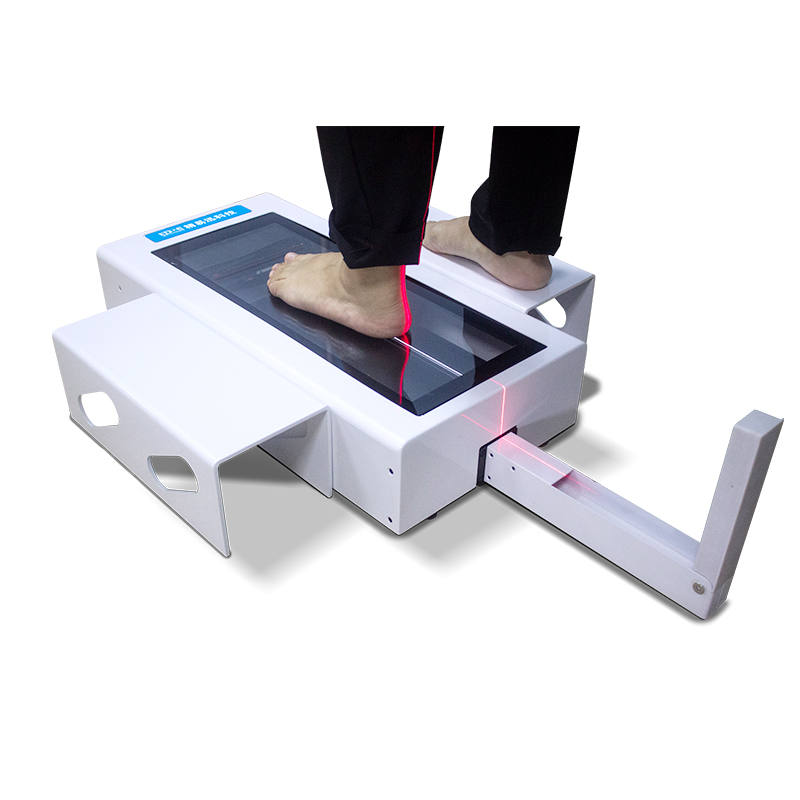
2. Convert data into design
After the scan is completed, the system will automatically generate a three-dimensional digital foot model. Technicians can further carry out personalized design based on this digital model: for example, adjust the support curve according to the height of the arch of the foot; optimize the thickness layout of the insole according to the stress area of the sole of the foot.
This process truly achieves “different for each person”, and every detail is tailored for your feet.
3. 3D printing, achieving precision like mass production
With accurate design data, it is the turn of 3D printing technology. 3D printing can be stacked layer by layer at the millimeter level, accurately reproducing the shape of the designed insole, whether it is a complex curved surface or a subtle support structure, it can be restored one by one.
More importantly, 3D printing has a variety of material options. It can use soft and comfortable elastic materials to improve the wearing experience, and can also increase stiff areas as needed to provide effective support and correction. The entire production cycle is also very short. From design to finished product, it only takes a few hours to one or two days, which is much faster than traditional processes.
4. Real “Personal Customization”, Change Starts from the Foot
Through the combination of 3D scanning of the soles of the feet and 3D printing, each pair of insoles contains the power of technology and also embodies the care for the feet. It is no longer the same standard size on the market, no longer a compromise and accommodation, but a true fit, support, and comfort, which comprehensively improves the experience of daily walking and exercise.
Whether it is people who often need to stand for a long time or walk for a long time, or people with minor foot problems who hope to improve their posture through insoles, they can find a solution suitable for them in this set of technological processes