In the custom insole industry, efficiency and precision have always been the two cores. The traditional process of “one-to-one slow measurement” in the past seems to be unable to cope with the rapid growth of customer volume. Especially in centralized scanning scenarios such as hospitals, physical examination institutions, and rehabilitation centers, how to achieve efficient and high-precision data collection has become a key bottleneck restricting production capacity.
The good news is that the three-dimensional laser scanning technology of the sole is bringing new breakthroughs to insole customizers. Through the automated solution of batch scanning, you can make the entire collection process as efficient and standardized as an assembly line, and – without sacrificing accuracy.
Today, let’s talk about how insole companies can use this technology to achieve batch speed-up from “measurement to model”.
What is three-dimensional laser scanning? Why is it suitable for the customized industry?
A three-dimensional laser scanner is a high-precision acquisition device based on optical recognition technology. It scans the surface of the sole of the foot with a high-speed laser beam to generate a complete three-dimensional model. The advantages of this technology are:
Non-contact measurement, safer and more hygienic
Short scanning time, only 5 seconds for one person
Complete data, model clarity up to 0.5 mm
Automatic modeling, convenient for subsequent design docking
Especially suitable for insole customization scenarios that require large-scale and accurate collection of foot shape data.
Pain points of traditional methods in batch scanning scenarios
Have you encountered these problems:
Customers queue up for scanning, waiting time is too long
Operators’ manual operation is cumbersome and inefficient
Data export is chaotic, and it is difficult to match seats later
The number of customers is large, and there is no time to model and process
In the final analysis, the traditional scanning method is too dependent on manual labor and lacks systematic management.
Automated solutions make scanning as efficient as a factory
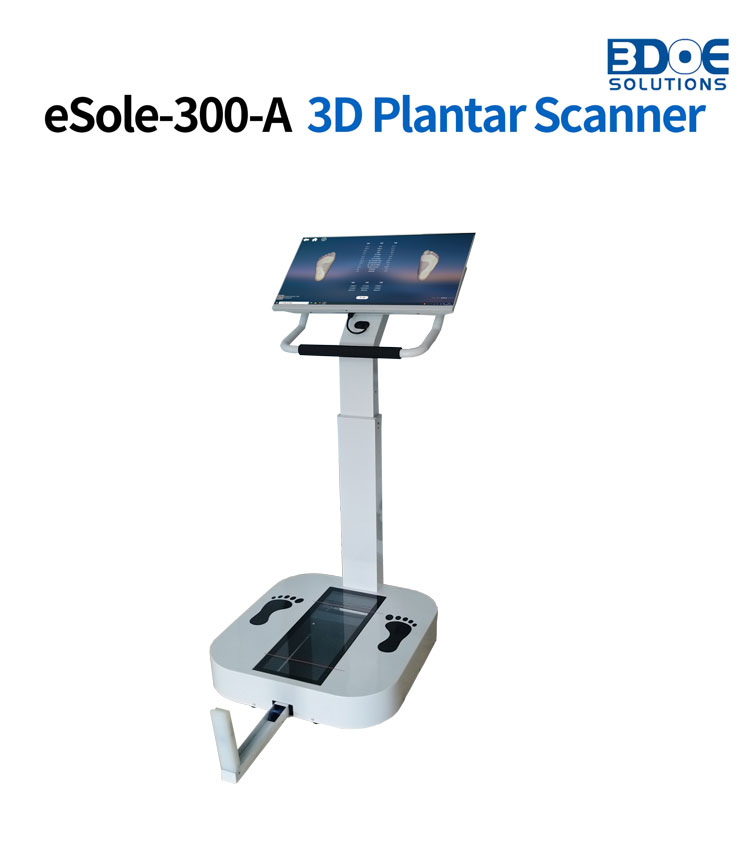
The core of the new batch scanning solution lies in the integrated collaboration of equipment + software + management system. It mainly includes the following modules:
1. Multi-station laser scanning station
Multiple independent sites can be set up to support multiple people scanning at the same time, which is suitable for outpatient peak or corporate group collection. Each site is equipped with an independent laser system without interfering with each other.
2. Automatic control of the scanning process
After the customer stands on the scanning platform, the system automatically recognizes the standing posture and starts scanning, without manual buttons or operations, improving labor efficiency.
3. Real-time data upload and number matching
Each customer is bound to a unique number (can be identified by QR code, mobile phone number or ID card), and the scanning results are automatically archived and uploaded to the cloud or local database to ensure that the data is not confused.
4. Rapid model generation and docking with the modeling platform
After the scan is completed, the system automatically outputs a standard 3D model file, which supports seamless docking with a variety of insole design software without manual export or format conversion.
Cost and return: equipment investment, double efficiency
Perhaps you are worried about the cost issue. But imagine:
Originally, only 10 people could be scanned in 1 hour, but now more than 50 people can be scanned
The number of operators is reduced by half, and the labor cost is significantly saved
Data processing is standardized, customer satisfaction and repurchase rate are improved
Systematic management is more conducive to store chain expansion and data analysis
This is not only an equipment upgrade, but also an upgrade of the business model.