As foot health management gradually enters the era of “refinement” and “dataization,” 3D foot scanners are increasingly favored by shoe stores, rehabilitation institutions, and orthopedic centers.
These devices not only quickly capture three-dimensional data of various parts such as the foot sole, foot dorsum, and foot arch, but also provide structural support for insole customization, shoe model recommendation, and gait analysis.
This brings up an important question—can ordinary people operate such high-tech equipment directly? Is professional training required?
The answer is: Yes, it is definitely needed, and the more professional the operation, the greater the value!
1. A 3D foot scanner is not as simple as “just a quick scan”
Many people mistakenly think that operating a 3D scanner is like using a barcode reader—just open the software, aim at the foot, press a button, and the scan is done. But in reality, every step from preparation to operation to data interpretation requires professional knowledge.
For example, before scanning, the customer must maintain the correct standing or sitting posture; otherwise, the foot data may be distorted. During the scanning process, even a slight movement of the foot may affect the accuracy of the 3D model. After scanning, one must also be able to judge the arch height, toe bone alignment, heel inclination angle, and other structural indicators—none of which are immediately obvious or easy to understand.
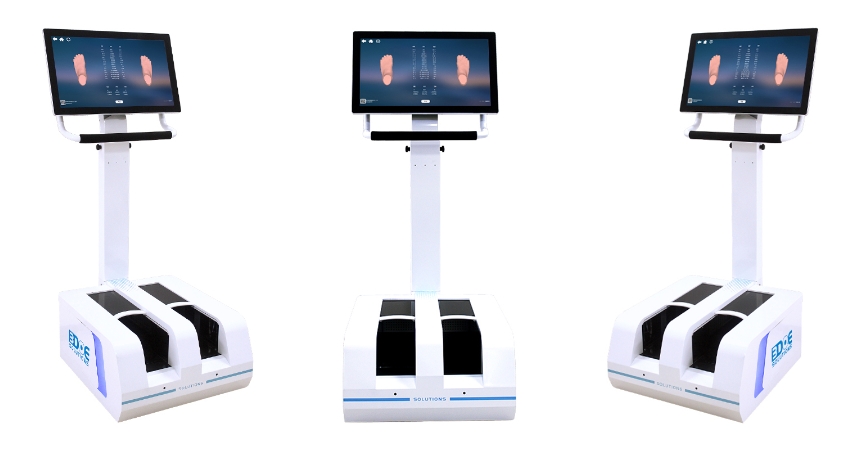
2. Incorrect operation can directly lead to inaccurate assessments
The greatest value of a 3D foot scan lies in providing accurate data references for personalized interventions. If the operation is not standardized—such as a skewed scanning angle, incorrect software parameters, or failure to calibrate in advance—the following issues may arise:
- Significant deviation between scan data and the actual foot shape
- Toe shadow duplication, abnormal arch collapse angle
- Misleading output reports that result in incorrect orthotic or insole design
Once the data is wrong, all subsequent insole production, gait intervention, and product recommendations may be “off track,” potentially worsening foot problems instead of solving them.
3. Receiving training is not a “waste of time,” but rather “worth every minute”
Currently, many equipment manufacturers and foot health service platforms provide accompanying training courses, including:
- Proper use of scanner hardware and software
- Posture preparation before scanning
- Basic knowledge of foot anatomy
- Interpretation and analysis of 3D data
- Techniques for combining and interpreting data with foot pressure measurements
Operators who undergo systematic training can not only collect data accurately, but also provide preliminary interpretation of the scan images and offer more professional advice to clients—truly turning the device into an extension of service.
4. The more knowledgeable you are, the easier it is to gain customer trust
In today’s increasingly competitive industry, equipment is no longer the barrier. The real core advantage lies in “those who understand the equipment and can interpret the data.” When customers see a highly skilled and professional operator handling a high-end 3D scanner, they naturally build trust. In contrast, a staff member who operates clumsily and can’t explain the results may lead customers to think, “This is just a gimmick, not professionalism.”
Pingback: Foot Scanner_Foot Shape Scanner_Gait Analysis Equipment_Gait Analyzer Manufacturer_Gait Analysis System